Coastal Outdoor Elevators A Comprehensive Guide
Coastal Outdoor Elevators represent a unique engineering challenge, blending the need for accessibility with the harsh realities of a coastal environment. Salt air corrosion, high humidity, and potential for extreme weather events necessitate specialized design and robust maintenance strategies. This guide delves into the market analysis, design considerations, operational aspects, environmental impact, regulatory compliance, and cost analysis associated with these specialized elevators.
We’ll explore the various materials, safety features, and sustainable practices that contribute to their successful implementation and longevity in demanding coastal locations.
From understanding the current market landscape and identifying key players to examining the intricate details of design, maintenance, and regulatory compliance, we aim to provide a thorough understanding of coastal outdoor elevators. We will also explore the environmental considerations and the financial aspects, including return on investment, to provide a holistic perspective on this niche but important sector.
Market Analysis of Coastal Outdoor Elevators
The market for coastal outdoor elevators is a niche but growing sector within the broader elevator industry. Driven by increasing coastal populations, luxury waterfront property development, and a need for accessible beachfront access, this specialized market segment presents unique opportunities and challenges. This analysis explores the current market size, key players, elevator types, and material considerations for this specialized industry.
Current Market Size and Growth Potential
Precise market sizing for coastal outdoor elevators is difficult due to the lack of dedicated market research reports focusing solely on this niche. However, we can infer growth based on broader trends. The global elevator market is experiencing steady growth, fueled by urbanization and infrastructure development. Coastal regions, particularly in affluent areas, are seeing increased demand for luxury homes and improved accessibility.
This demand, coupled with the increasing popularity of waterfront properties, suggests a significant, albeit currently unquantified, growth potential for coastal outdoor elevators. For example, the increasing number of high-end residential developments in coastal areas of Florida, California, and the Mediterranean show a clear correlation between luxury property and the need for specialized outdoor elevators. We can reasonably project moderate to high growth in this sector over the next decade, mirroring, and potentially exceeding, the growth of the luxury coastal real estate market.
Coastal outdoor elevators offer stunning views, especially during festive seasons. For example, imagine the breathtaking panorama while you’re decorating for Halloween; you could even use the elevator to easily transport your heavier Outdoor Halloween Decorations to the rooftop for optimal display. Then, after the festivities, the elevator provides convenient access for dismantling your spooky setup. This makes coastal outdoor elevators even more appealing.
Key Players and Market Share, Coastal Outdoor Elevator
Identifying precise market share data for coastal outdoor elevator manufacturers is challenging due to the fragmented nature of the market. Many established elevator companies offer custom solutions for coastal environments, but they rarely break down their sales figures specifically for this niche. However, major elevator manufacturers like ThyssenKrupp, Otis, and Kone are likely significant players, offering specialized designs and materials to withstand coastal conditions.
Smaller, specialized firms focusing exclusively on outdoor and marine elevator solutions also exist, though their market share is likely less significant than the larger players. Further research into company financial reports and industry publications would be needed for more accurate market share estimations.
Comparison of Elevator Types Suitable for Coastal Environments
Several elevator types are suitable for coastal environments, each with its own advantages and disadvantages. Hydraulic elevators, while offering smooth operation, are susceptible to corrosion from saltwater exposure and require careful maintenance. Traction elevators, utilizing steel ropes and a motor, are generally more robust and less prone to corrosion, making them a popular choice. Pneumatic elevators, using compressed air, offer a unique solution but may require specialized designs for coastal environments to prevent moisture ingress.
The optimal choice depends on factors such as building height, passenger capacity, budget, and specific environmental conditions. For example, a high-rise luxury condominium might opt for a robust traction elevator system, while a smaller beachfront property might find a hydraulic or pneumatic system more cost-effective.
Material Selection for Coastal Elevator Construction
The choice of materials is crucial for ensuring the longevity and safety of coastal outdoor elevators. Exposure to saltwater, humidity, and UV radiation necessitates the use of corrosion-resistant and weather-resistant materials.
Material | Advantages | Disadvantages | Suitability for Coastal Environments |
---|---|---|---|
Stainless Steel | High corrosion resistance, strength, durability | High cost, can be heavy | Excellent |
Aluminum | Lightweight, corrosion resistant (with proper coatings), relatively inexpensive | Lower strength compared to steel, susceptible to scratching | Good (with appropriate surface treatments) |
Galvanized Steel | Cost-effective, good corrosion resistance | Requires regular maintenance, zinc coating can wear off over time | Moderate (requires regular inspection and maintenance) |
Marine-Grade Composites | Lightweight, high strength-to-weight ratio, corrosion resistant | Can be more expensive than steel, may require specialized fabrication techniques | Excellent |
Design Considerations for Coastal Outdoor Elevators
Designing outdoor elevators for coastal environments presents unique challenges due to the harsh conditions. Salt air, high humidity, and potential for strong winds and storms necessitate robust construction and specialized materials to ensure longevity, safety, and reliable operation. Careful consideration of these factors is paramount to the success of any coastal outdoor elevator project.
Challenges Posed by Coastal Environments
The corrosive nature of salt air is a primary concern. Salt particles readily adhere to metal surfaces, accelerating rust and corrosion. High humidity promotes the growth of mold and mildew, potentially compromising the structural integrity of the elevator components and impacting its mechanical functionality. Furthermore, coastal regions are often subjected to strong winds and even hurricanes, requiring the elevator structure to withstand significant forces.
These factors necessitate the use of corrosion-resistant materials and robust structural design to ensure the elevator’s lifespan and safety. For example, stainless steel components, specialized coatings, and reinforced structural elements are crucial to mitigate these challenges.
Safety Features and Compliance Requirements
Coastal outdoor elevators must adhere to stringent safety standards, often exceeding those required for inland elevators. These regulations typically address wind load resistance, corrosion protection, emergency power systems, and accessibility requirements. Compliance often involves rigorous testing and certification processes to ensure the elevator operates safely and reliably in challenging coastal conditions. For instance, emergency lighting and communication systems are critical, especially during power outages or severe weather events.
Regular inspections and maintenance are also vital to address any corrosion or wear and tear. Compliance with the Americans with Disabilities Act (ADA) is also essential, ensuring accessibility for people with disabilities.
Hypothetical Coastal Outdoor Elevator Design
A hypothetical coastal outdoor elevator might utilize a stainless steel structure with a marine-grade powder coating for enhanced corrosion resistance. Dimensions could be approximately 3 meters by 2 meters, with a capacity of 10 people. The elevator car would be constructed from durable, weather-resistant materials, possibly incorporating tempered glass for visibility and natural light. Safety features would include multiple emergency stop buttons, a backup power system, robust wind bracing, and a sophisticated monitoring system to detect and alert maintenance personnel to potential issues.
The elevator mechanism would be enclosed within a weatherproof housing, protecting it from the elements. Emergency lighting and communication systems would be integrated into the design, and the elevator would be compliant with all relevant safety standards and accessibility requirements.
Visual Representation of an Accessible Coastal Elevator
Imagine a sleek, modern elevator with a stainless steel exterior, seamlessly integrated into a coastal landscape. The elevator car is spacious, featuring ample room for wheelchairs and other mobility devices. Tactile signage and audible announcements provide clear guidance for visually impaired users. Large, clear buttons with Braille markings ensure ease of use for all. Handrails are strategically positioned, providing secure support for passengers.
The elevator doors open smoothly and widely, eliminating any potential obstacles for wheelchair users or those with other mobility challenges. The elevator’s design is not only functional but also aesthetically pleasing, complementing the surrounding coastal environment. The overall design prioritizes safety, accessibility, and durability in the harsh coastal climate.
Coastal outdoor elevators offer convenient access to elevated coastal properties, enhancing both accessibility and luxury. The overall aesthetic, however, extends beyond the elevator itself; consider complementing the coastal vibe with stylish Front Door Decor to create a cohesive and welcoming entrance. This ensures that the journey to your elevated coastal home is visually appealing from the very beginning, reflecting the high standards of the elevator itself.
Maintenance and Operation of Coastal Outdoor Elevators
The longevity and safe operation of coastal outdoor elevators hinge on a robust maintenance program tailored to the unique challenges of the marine environment. Salt spray, humidity, and strong winds all contribute to accelerated wear and tear, demanding proactive strategies to mitigate potential issues and ensure passenger safety. This section details best practices for maintenance, Artikels potential problems specific to coastal locations, and provides a sample preventative maintenance schedule.
Best Practices for Maintaining Coastal Outdoor Elevators
Regular inspection and preventative maintenance are paramount. Elevators situated near the coast require more frequent attention than those in inland locations. A key element is thorough cleaning to remove salt deposits and corrosive residues that accumulate on all elevator components. This includes the elevator car, hoistway, guide rails, and electrical components. Using specialized cleaning solutions designed for marine environments is recommended to avoid damaging sensitive parts.
Furthermore, lubrication of moving parts should be more frequent, using marine-grade lubricants resistant to corrosion and salt water. Regular inspections should focus on checking for corrosion, rust, and signs of wear on cables, pulleys, and other critical components. Finally, meticulous documentation of all maintenance activities is crucial for tracking performance and identifying potential problems early.
Potential Maintenance Issues Specific to Coastal Locations and Their Solutions
Coastal environments present several unique challenges. Salt spray accelerates corrosion on metal components, leading to premature failure. Regular washing with freshwater and the application of corrosion inhibitors can significantly extend the lifespan of metal parts. Humidity can cause electrical problems, such as short circuits and insulation breakdown. Regular inspection of electrical wiring and components, along with the use of weatherproof seals and coatings, is essential.
Strong winds can cause damage to the elevator car and hoistway doors. Reinforcing these structures and ensuring proper sealing can prevent wind damage. Finally, the ingress of sand and debris can lead to mechanical malfunctions. Regular cleaning and the use of appropriate sealing measures can minimize these issues.
Preventative Maintenance Schedule for a Coastal Outdoor Elevator
A comprehensive preventative maintenance schedule is crucial for minimizing downtime and extending the elevator’s lifespan. This schedule should be tailored to the specific elevator model and local conditions.
Task | Frequency | Notes |
---|---|---|
Visual Inspection (Exterior & Interior) | Daily | Check for damage, corrosion, and unusual noises. |
Cleaning (Salt Removal) | Weekly | Use appropriate cleaning solutions for marine environments. |
Lubrication of Moving Parts | Monthly | Use marine-grade lubricants. |
Electrical System Inspection | Quarterly | Check wiring, connections, and safety devices. |
Comprehensive Mechanical Inspection | Semi-Annually | Inspect cables, pulleys, brakes, and other critical components. |
Professional Service & Inspection | Annually | Thorough inspection and maintenance by qualified technicians. |
Emergency Repair Procedures and Safety Protocols
In case of a malfunction, immediate action is necessary to ensure passenger safety. Emergency stop buttons should be readily accessible and clearly marked. A clear communication system should be in place to contact emergency services and maintenance personnel. The elevator should be equipped with an emergency lighting system and a means of communication within the elevator car.
Procedures for rescuing trapped passengers should be established and regularly practiced by maintenance personnel. Furthermore, a detailed emergency response plan should be in place, including contact information for relevant authorities and maintenance teams. Regular safety drills and training for personnel involved in elevator operation and maintenance are essential.
Environmental Impact and Sustainability
Coastal outdoor elevators, while offering convenient access to coastal areas, present unique environmental considerations throughout their lifecycle. Minimizing their impact requires careful attention to material selection, energy efficiency, and responsible disposal practices. This section explores the environmental footprint of these elevators and Artikels strategies for sustainable design and operation.The environmental impact of coastal outdoor elevators stems from several key areas: the manufacturing process, operational energy consumption, and eventual decommissioning and disposal.
Manufacturing involves resource extraction, energy-intensive production processes, and potential emissions from transportation. Operational energy consumption is influenced by the type of power source used, while decommissioning involves waste generation and the need for responsible material recycling or disposal. Understanding these impacts allows for informed decisions regarding sustainable design and operation.
Manufacturing and Material Selection
Sustainable material choices significantly influence the elevator’s overall environmental footprint. Using recycled steel, sustainably sourced timber (certified by organizations like the Forest Stewardship Council), and aluminum – known for its recyclability – reduces the demand for virgin materials and minimizes carbon emissions associated with extraction and processing. Furthermore, employing low-VOC (volatile organic compound) paints and coatings reduces air pollution during manufacturing and minimizes harmful emissions during the elevator’s lifespan.
The selection of durable materials also extends the elevator’s operational life, further reducing the need for replacement and associated environmental impact. For example, using marine-grade stainless steel for external components minimizes corrosion and reduces the need for frequent maintenance and repairs.
Energy-Efficient Technologies and Power Sources
The choice of power source significantly impacts the operational energy consumption and, consequently, the carbon footprint of the elevator. Electric elevators, powered by renewable energy sources such as solar or wind power, offer a significantly lower environmental impact compared to hydraulic elevators. Hydraulic systems rely on hydraulic fluid, which can be harmful to the environment if leaked. Moreover, electric motors are generally more efficient than hydraulic systems, reducing energy consumption and operating costs.
Incorporating energy-efficient components, such as regenerative braking systems (which recapture energy during descent and feed it back into the power grid), further minimizes energy consumption. A well-designed control system that optimizes energy usage based on demand also contributes to reduced energy consumption.
Comparison of Elevator Power Sources
Power Source | Environmental Impact | Advantages | Disadvantages |
---|---|---|---|
Hydraulic | Higher environmental impact due to hydraulic fluid production and potential leaks; higher energy consumption. | Simpler design, potentially lower initial cost. | Fluid leaks can contaminate soil and water; less energy-efficient; requires more frequent maintenance. |
Electric | Lower environmental impact, especially with renewable energy sources; higher energy efficiency. | Energy efficient; lower maintenance; quieter operation. | Higher initial cost; more complex design. |
Strategies to Minimize Environmental Impact
Minimizing the environmental impact of coastal outdoor elevators requires a holistic approach throughout their lifecycle. The following strategies are crucial:
- Sustainable Material Selection: Prioritize recycled and sustainably sourced materials whenever possible, opting for durable, long-lasting components to reduce the need for replacements.
- Energy-Efficient Design: Incorporate energy-efficient technologies such as regenerative braking systems and optimized control systems to minimize energy consumption.
- Renewable Energy Integration: Power the elevator with renewable energy sources like solar or wind power whenever feasible.
- Responsible Waste Management: Implement a comprehensive plan for the responsible recycling or disposal of components at the end of the elevator’s lifespan, minimizing waste sent to landfills.
- Lifecycle Assessment: Conduct a comprehensive lifecycle assessment (LCA) to identify and quantify the environmental impacts of the elevator at each stage of its life, from manufacturing to disposal, to inform design choices and operational practices.
- Optimized Maintenance: Regular and preventative maintenance extends the lifespan of the elevator and reduces the need for replacements, minimizing environmental impact.
Regulatory Compliance and Building Codes
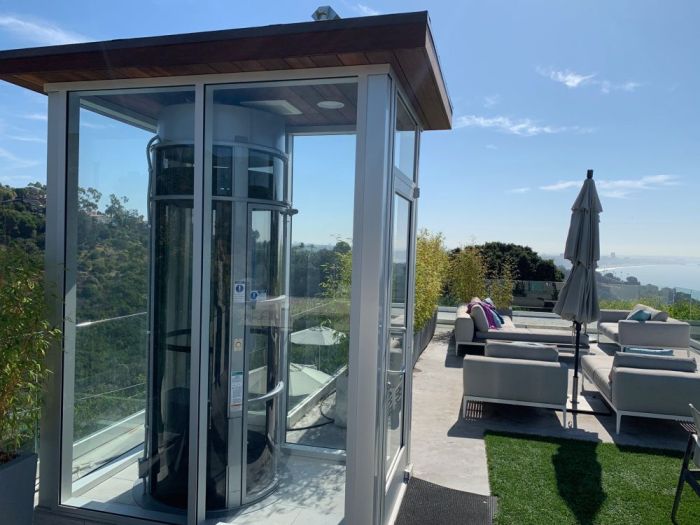
Source: vacuumelevators.com
Coastal outdoor elevators offer stunning views, especially during festive seasons. For instance, imagine enjoying a breathtaking sunset while planning your spooky outdoor décor; perhaps you’ll find inspiration browsing Select Outdoor Halloween Decorations for your coastal home. The convenience of a coastal outdoor elevator ensures easy access to all levels, perfect for admiring your Halloween display.
Installing a coastal outdoor elevator requires careful consideration of numerous building codes and regulations designed to ensure public safety and accessibility. These regulations vary significantly depending on location, encompassing both national and local ordinances, and often incorporate specific provisions addressing the unique challenges posed by coastal environments. Navigating this complex regulatory landscape is crucial for successful project completion.The permitting process for a coastal outdoor elevator is multifaceted and involves several key steps.
First, detailed plans and specifications must be submitted to the relevant authorities, typically including the local building department and potentially other agencies such as coastal zone management or environmental protection boards. These submissions need to demonstrate compliance with all applicable building codes and regulations. Following submission, a thorough review process ensues, which may involve site inspections and consultations with engineers and other specialists.
Upon successful review and approval, the necessary permits are issued, allowing construction to commence. Failure to obtain the proper permits before starting construction can lead to significant delays and potential legal repercussions.
Permitting Process for Coastal Outdoor Elevators
The permitting process generally involves several stages: initial application submission with complete plans and specifications, a review period where the application is assessed for compliance, potential requests for revisions or additional information, a site inspection to verify compliance, and finally, the issuance of building permits upon successful completion of all review stages. Specific timelines vary depending on the jurisdiction and the complexity of the project.
It’s advisable to initiate the permitting process well in advance of the intended construction start date to account for potential delays. Consulting with experienced professionals familiar with local regulations can significantly streamline this process.
Necessary Inspections and Certifications
Once construction is complete, a series of inspections are required to verify that the installed elevator meets all safety and accessibility standards. These inspections typically cover various aspects of the elevator system, including the mechanical components, electrical systems, safety devices, and accessibility features. Upon successful completion of these inspections, a certificate of occupancy or a similar certification is issued, confirming that the elevator is compliant with all applicable regulations and is safe for operation.
Regular inspections and maintenance are also typically required to ensure ongoing compliance and safety.
Relevant Building Codes and Regulations for Safety and Accessibility
Coastal outdoor elevators must adhere to various building codes and regulations, emphasizing safety and accessibility. For example, the International Building Code (IBC) and the Americans with Disabilities Act (ADA) Standards for Accessible Design provide crucial guidelines. The IBC addresses structural integrity, fire safety, and other crucial safety aspects in the design and construction of elevators, while the ADA ensures accessibility for people with disabilities.
Specific coastal regulations may also mandate additional requirements, such as resistance to corrosion, wind loads, and potential flooding. These regulations often require the use of specific materials and construction techniques to ensure the longevity and safety of the elevator in the harsh coastal environment. For example, the use of marine-grade stainless steel or other corrosion-resistant materials is often mandated to withstand the effects of salt spray and humidity.
Cost Analysis and Return on Investment
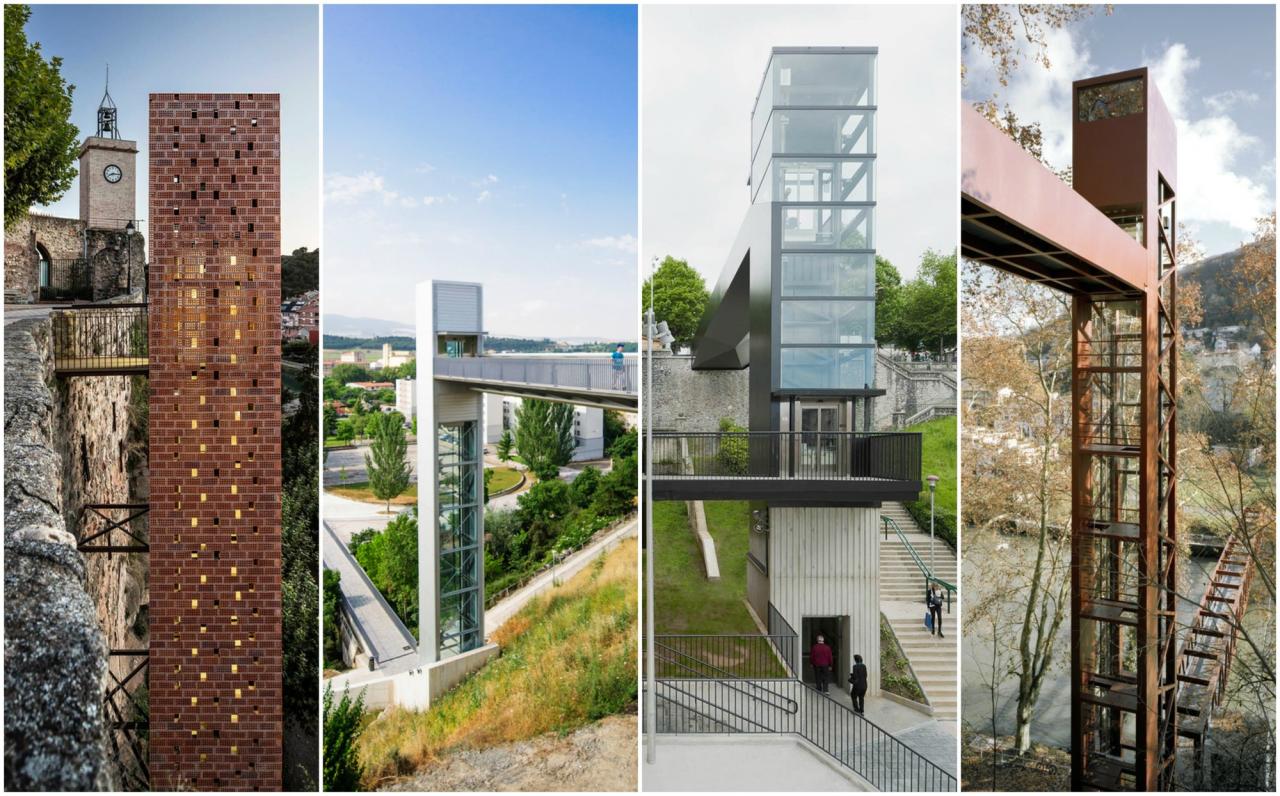
Source: adsttc.com
Investing in a coastal outdoor elevator requires a thorough understanding of associated costs and potential returns. This analysis will break down the expenses involved in purchasing, installing, and maintaining such an elevator, illustrating how to calculate return on investment (ROI) and comparing different elevator types. We will focus on a specific scenario – a beachfront property – to provide a concrete example.
Cost Breakdown of Coastal Outdoor Elevators
The total cost of a coastal outdoor elevator project encompasses several key components. These include the elevator itself, installation, site preparation, foundation work, permits and inspections, ongoing maintenance, and potential future repairs. The price of the elevator varies significantly depending on factors such as capacity, height, materials (stainless steel is common for coastal environments due to its corrosion resistance), and features (e.g., accessibility features).
Coastal outdoor elevators offer stunning views, but their surroundings often need enhancement. To complement the elevator’s aesthetic, consider incorporating visually appealing wall decor near the access point. For inspiration, check out 17 Best Creative Wall Decoration Ideas to Transform Your Space for ideas to elevate the overall experience. The right wall treatment can seamlessly blend the elevator into its coastal setting.
Installation costs depend on site accessibility and complexity. Site preparation might include leveling the ground, creating a suitable base, and addressing drainage issues specific to coastal locations. Permits and inspections are governed by local building codes and regulations, which can vary significantly. Finally, ongoing maintenance is crucial in a harsh coastal environment, requiring regular inspections, lubrication, and potential component replacements.
Coastal outdoor elevators offer convenient access to elevated coastal properties, enhancing both functionality and aesthetic appeal. Their design can be seamlessly integrated with your home’s overall style, complementing the seasonal changes reflected in your decor, perhaps drawing inspiration from Seasonal Home Decor Ideas to create a cohesive look. Ultimately, a well-designed coastal outdoor elevator becomes a key feature, enhancing the enjoyment of your coastal home year-round.
Return on Investment (ROI) Calculation for a Beachfront Property
Let’s consider a hypothetical beachfront property with a two-story house. A hydraulic elevator with a capacity of 500 kg and a travel distance of 6 meters might cost approximately $50,000 – $80,000 for the elevator itself. Installation, including site preparation and foundation work, could add another $20,000 – $40,000. Permits and inspections might range from $5,000 to $10,000 depending on location.
Therefore, the total initial investment could be between $75,000 and $130,000.Annual maintenance costs could range from $2,000 to $5,000, depending on the frequency of inspections and any necessary repairs.To calculate ROI, we need to consider the increased property value and potential rental income. A coastal outdoor elevator can significantly enhance a property’s value, potentially increasing its sale price by 10-20% or more.
Coastal outdoor elevators offer unparalleled access to stunning coastal views, transforming beachfront properties. The cost of such a luxurious addition can be significant, however, so consider offsetting expenses by creatively furnishing the surrounding areas with pre-loved pieces; you might be surprised by the unique finds available when exploring the world of Thrifting Furniture. This approach not only saves money but adds character, complementing the modern elegance of your coastal outdoor elevator installation.
Moreover, it can attract higher rental income, especially from guests with mobility challenges. Assuming a 15% increase in property value ($11,250 to $19,500 on a $75,000 to $130,000 investment) and an additional $5,000 annual rental income, the ROI can be calculated over a specific timeframe (e.g., 10 years).
ROI = (Total Return – Total Investment) / Total Investment – 100%
The precise ROI will depend on several factors, including the specific location, property value, rental income, and maintenance costs. A detailed financial projection should be created for each individual project.
Comparison of Elevator Types and Long-Term Maintenance
Different elevator types, such as hydraulic, traction, and pneumatic, each have varying initial costs and long-term maintenance requirements. Hydraulic elevators are generally less expensive initially but might require more frequent maintenance due to the hydraulic fluid and associated components. Traction elevators are typically more expensive upfront but may have lower long-term maintenance costs. Pneumatic elevators are a more specialized option, often suitable for low-rise applications, with their own set of cost and maintenance considerations.
The choice of elevator type should be based on a comprehensive cost-benefit analysis considering factors such as initial investment, operating costs, maintenance requirements, and longevity. In coastal environments, the material selection (stainless steel is preferable for corrosion resistance) significantly impacts long-term maintenance.
Cost Factors for a Coastal Elevator Project
Cost Factor | Low Estimate | High Estimate | Notes |
---|---|---|---|
Elevator Purchase | $50,000 | $80,000 | Varies based on size, capacity, and features. |
Installation | $20,000 | $40,000 | Includes site preparation, foundation, and electrical work. |
Permits & Inspections | $5,000 | $10,000 | Dependent on local regulations. |
Annual Maintenance | $2,000 | $5,000 | Covers inspections, lubrication, and minor repairs. |
Final Review
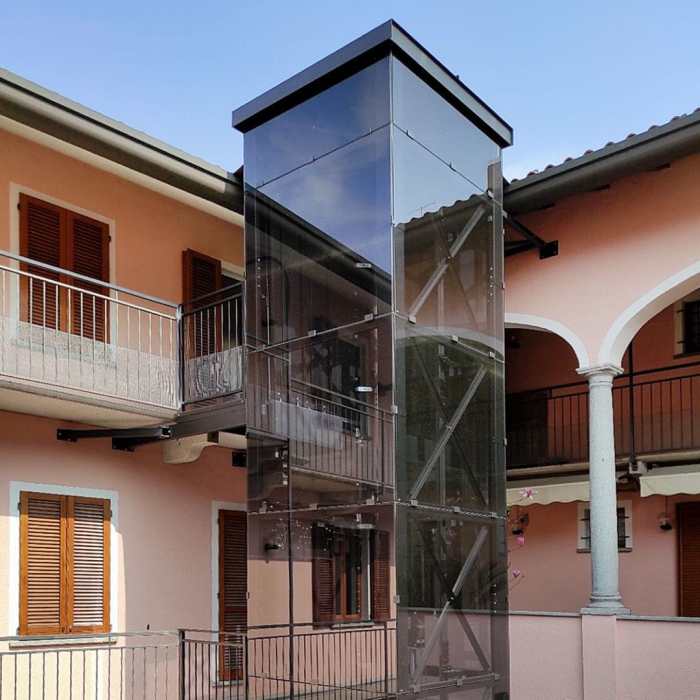
Source: archiexpo.com
Coastal outdoor elevators present a compelling blend of engineering innovation and environmental responsibility. Successfully navigating the unique challenges posed by coastal environments requires a multi-faceted approach, encompassing careful design, rigorous maintenance, and adherence to stringent regulations. By understanding the market dynamics, considering sustainable practices, and analyzing the cost-benefit aspects, stakeholders can effectively deploy these crucial access solutions while minimizing environmental impact and maximizing long-term value.
The careful consideration of all these factors is key to ensuring the safe, reliable, and environmentally conscious operation of coastal outdoor elevators for years to come.
FAQ: Coastal Outdoor Elevator
What are the typical lifespan of coastal outdoor elevators?
Lifespan varies greatly depending on materials, maintenance, and environmental exposure. With proper maintenance, a well-designed elevator can last 20-30 years or more.
What types of power sources are commonly used?
Electric and hydraulic systems are both common. Electric systems are generally preferred for their efficiency and reduced environmental impact.
Are there specific insurance requirements for coastal outdoor elevators?
Yes, insurance requirements will vary by location and the specific risks involved. It’s crucial to consult with insurance professionals to determine the appropriate coverage.
How often should inspections be conducted?
Regular inspections, typically monthly or quarterly, are essential, with more frequent checks during periods of severe weather or high usage.
What are the implications of non-compliance with building codes?
Non-compliance can lead to significant fines, operational shutdowns, and legal liability in case of accidents or injuries.