Commercial Exterior Elevators A Comprehensive Guide
Commercial Exterior Elevators: These architectural marvels seamlessly blend functionality with aesthetics, offering convenient vertical transportation for various building types. From sleek glass enclosures gracing modern office towers to robust freight elevators serving industrial complexes, exterior elevators present unique design and engineering challenges. This guide delves into the diverse aspects of commercial exterior elevators, covering their various types, safety features, maintenance requirements, design considerations, cost implications, accessibility compliance, and environmental impact.
We’ll explore the intricacies of these vital building components, providing a thorough understanding for architects, engineers, building owners, and anyone interested in this specialized field.
This comprehensive exploration covers everything from the different types of commercial exterior elevators—passenger, freight, and service—and their specific applications, to the critical safety features and regulations governing their installation and operation. We’ll also delve into the crucial aspects of maintenance and repair, ensuring smooth and safe operation, and explore the design considerations that influence both aesthetics and functionality. The financial aspects, including initial costs, ongoing maintenance, and budgeting, will be addressed, along with the importance of adhering to ADA accessibility guidelines and minimizing the environmental impact of these essential systems.
Types of Commercial Exterior Elevators
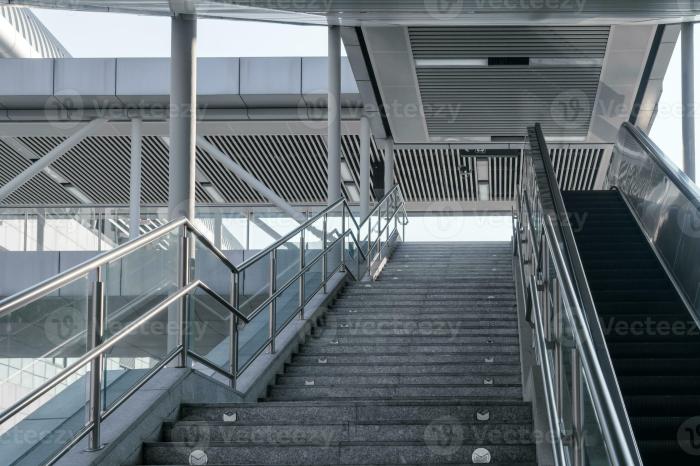
Source: vecteezy.com
Exterior elevators offer a unique solution for multi-story commercial buildings, providing convenient vertical transportation while preserving valuable interior space. The choice of elevator type depends heavily on the building’s specific needs, including the volume and type of traffic, the overall aesthetic, and budget considerations. Understanding the differences between available options is crucial for making informed decisions.
Commercial Exterior Elevator Types
The following table summarizes the key differences between common types of commercial exterior elevators.
Type | Capacity | Common Uses | Notable Features |
---|---|---|---|
Passenger Elevator | Varies, typically 1,500-4,000 lbs (680-1814 kg) | Office buildings, hotels, retail spaces, residential high-rises | Enhanced comfort features (e.g., smooth ride, climate control), aesthetically pleasing design, often compliant with ADA accessibility standards. May incorporate safety features like emergency phones and lighting. |
Freight Elevator | Varies greatly, from several thousand pounds to tens of thousands of pounds | Warehouses, industrial buildings, loading docks, construction sites | Robust construction to handle heavy loads, often includes features for secure cargo handling (e.g., gates, ramps). May have higher load capacities and larger cabin sizes than passenger elevators. |
Service Elevator | Moderate capacity, typically less than passenger elevators but more than smaller dumbwaiters. | Hospitals, hotels, restaurants, office buildings (for internal transport of goods and materials). | Designed for efficient transport of goods and supplies, may include features for easy loading and unloading. Often smaller than freight elevators but larger than dumbwaiters. May have less emphasis on passenger comfort. |
Advantages and Disadvantages of Exterior Elevators
The selection of an exterior elevator involves weighing several factors. Cost, maintenance, and efficiency are paramount considerations.Passenger elevators, while offering a premium experience, typically come with a higher initial investment and ongoing maintenance costs compared to freight or service elevators. However, their efficiency in terms of passenger throughput can justify the expense in high-traffic commercial buildings. Freight elevators, due to their robust construction, are more expensive initially but can be highly efficient in their intended use cases, minimizing labor costs associated with manual material handling.
Service elevators provide a balance, offering a reasonable compromise between cost and functionality. Maintenance costs for all types are influenced by factors like environmental exposure and the frequency of use.
Design Considerations for Exterior Elevators
Exterior elevator design significantly impacts building aesthetics and accessibility.Passenger elevators often integrate seamlessly with the building’s exterior architecture, using materials and finishes that complement the overall design. Compliance with ADA (Americans with Disabilities Act) standards is crucial, ensuring accessibility features such as appropriate cabin size, button placement, and safety mechanisms. Freight and service elevators, while less focused on passenger aesthetics, still need to be integrated safely and effectively into the building’s design, often incorporating weatherproofing and security measures to protect equipment and contents.
Careful consideration of building codes and safety regulations is essential throughout the design and installation process for all elevator types.
Safety Features and Regulations
Commercial exterior elevators, while offering convenient access, require stringent safety measures to protect users and bystanders. Modern designs incorporate numerous features to mitigate risks and comply with building codes, ensuring a safe and reliable operation. These features are crucial, given the unique vulnerabilities associated with outdoor elevator installations.Safety features are not just about preventing accidents; they’re about minimizing the impact should an incident occur.
Modern systems combine mechanical safeguards with sophisticated electronic monitoring and communication systems, creating multiple layers of protection. This multifaceted approach ensures that even in the event of a malfunction, the consequences are significantly reduced.
Essential Safety Features, Commercial Exterior Elevators
Exterior elevators utilize a variety of safety mechanisms. Emergency brakes are a critical component, automatically engaging if the elevator encounters a malfunction or obstruction. These brakes are designed to be highly reliable and capable of quickly bringing the elevator to a safe stop. Independent safety systems, such as secondary braking mechanisms, provide redundancy to ensure a secure halt in case of primary brake failure.
Communication systems, including emergency phones and intercoms, allow trapped passengers to contact help, providing vital support during emergencies. These systems are typically connected to central monitoring stations, enabling rapid response. Overload protection mechanisms prevent the elevator from operating if the weight capacity is exceeded. These mechanisms may involve sensors, load cells, and automatic shutoff switches, ensuring the safety of both passengers and the elevator itself.
Regular maintenance and inspection of these features are vital for continued safety.
Relevant Safety Regulations and Building Codes
The installation and operation of exterior elevators are governed by comprehensive safety regulations and building codes, which vary by location but share common goals of ensuring user safety and preventing accidents. These regulations dictate everything from the design and construction of the elevator itself to the maintenance and inspection procedures that must be followed. Compliance is mandatory, and regular inspections are carried out to ensure adherence to these standards.
Non-compliance can result in significant penalties and legal repercussions.
- ASME A17.1/CSA B44: This is a widely adopted standard covering the safety requirements for elevators and escalators in North America. It details numerous safety features, testing procedures, and maintenance requirements.
- Local Building Codes: Municipal and regional building codes often incorporate or expand upon national standards, reflecting specific local conditions and requirements. These codes address issues such as accessibility, emergency access, and fire safety.
- OSHA Regulations (United States): The Occupational Safety and Health Administration (OSHA) sets standards for workplace safety, including the operation and maintenance of elevators. These regulations cover aspects like employee training, hazard identification, and emergency procedures.
- Accessibility Standards (ADA): The Americans with Disabilities Act (ADA) requires that elevators be accessible to people with disabilities. This includes requirements for button placement, door width, and cabin size.
Potential Safety Hazards and Mitigation Strategies
While modern safety features significantly reduce risks, certain hazards remain inherent in exterior elevator operation. Exposure to weather conditions such as wind, rain, and ice can affect elevator performance and safety. Regular inspections and maintenance, including weatherproofing measures, are crucial to mitigate these risks. Potential mechanical failures, while rare due to safety systems, can still occur. Regular maintenance, routine inspections, and the use of redundant safety systems minimize the likelihood of such failures and their consequences.
The possibility of vandalism or malicious damage is another concern. Robust construction, security systems (like cameras and alarms), and well-lit areas can help deter vandalism and improve safety. Finally, human error, including improper operation or maintenance, can lead to accidents. Thorough employee training, clear operating instructions, and regular safety audits are critical to minimize human error.
Maintenance and Repair
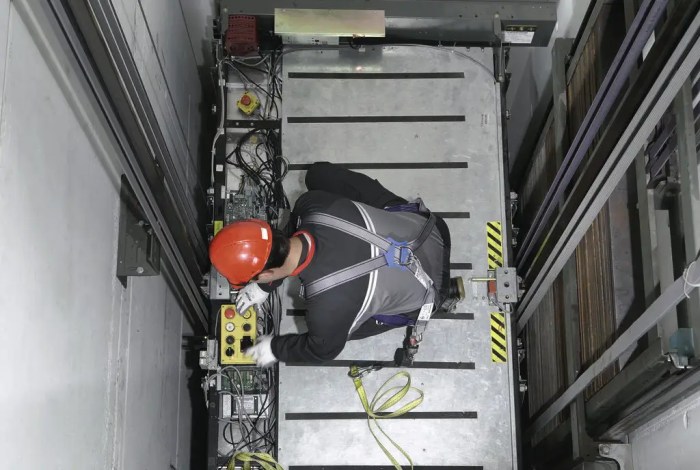
Source: dazenelevator.com
Keeping your commercial exterior elevator running smoothly and safely requires a proactive maintenance strategy. Neglecting regular upkeep can lead to costly repairs, downtime, and, most importantly, safety hazards. This section details the essential maintenance procedures, common problems, and the vital role of inspections and certifications.
Routine Maintenance Procedures
Regular maintenance is crucial for preventing major problems and ensuring the longevity of your exterior elevator. The following table Artikels key tasks, their frequency, procedures, and their importance for safe and efficient operation.
Maintenance Task | Frequency | Procedure | Importance |
---|---|---|---|
Lubrication of moving parts | Monthly | Apply appropriate lubricant to cables, sheaves, guides, and other moving components as per manufacturer’s recommendations. Ensure proper lubrication to reduce friction and wear. | Reduces friction, wear, and tear, extending the lifespan of components and preventing premature failure. |
Inspection of cables and ropes | Monthly | Visually inspect cables and ropes for fraying, corrosion, or damage. Check for proper tension. | Early detection of cable damage prevents catastrophic failures that could lead to serious injury or death. |
Cleaning of elevator car and hoistway | Weekly | Remove debris, dirt, and grime from the elevator car and hoistway. Pay close attention to areas that could impede movement or create safety hazards. | Maintains cleanliness and prevents accumulation of debris that could interfere with elevator operation or create safety risks. |
Testing of safety devices | Quarterly | Thoroughly test safety devices such as emergency brakes, limit switches, and safety gears according to manufacturer’s instructions. | Ensures that safety mechanisms function correctly in case of emergencies. |
Electrical system inspection | Annually | Inspect all electrical components for wear, damage, or loose connections. Test the electrical system for proper functionality. | Prevents electrical faults that could lead to malfunctions or fire hazards. |
Common Problems and Malfunctions
Exterior elevators, due to their exposure to the elements, are susceptible to specific problems. Understanding these issues and their solutions is crucial for minimizing downtime and ensuring passenger safety.
For example, water ingress can cause corrosion of electrical components and mechanical parts. This can lead to malfunctions and even complete elevator failure. Solutions include regular inspections for leaks, proper sealing of the hoistway, and the use of corrosion-resistant materials where appropriate.
Another common issue is wear and tear on the elevator’s guiding system. This can result in jerky movements and potential safety hazards. Regular lubrication and inspection of the guides are essential to prevent this problem. Severe wear may require replacement of components.
Wind load can also significantly impact exterior elevators, particularly in high-rise buildings or areas prone to strong winds. Regular checks of the elevator’s structural integrity and wind load capacity are essential. In extreme cases, wind mitigation measures may need to be implemented.
Importance of Regular Inspections and Certifications
Regular inspections and certifications are not merely recommendations; they are legal requirements in most jurisdictions. These inspections are conducted by qualified elevator inspectors who assess the elevator’s safety and compliance with relevant regulations. The process typically involves a thorough examination of all elevator components, a functional test, and the issuance of a certificate of compliance if the elevator meets all safety standards.
Failure to obtain and maintain certification can result in significant fines and potential legal liabilities. The certification process ensures that the elevator operates safely and reliably, protecting both passengers and building owners.
Design and Aesthetics
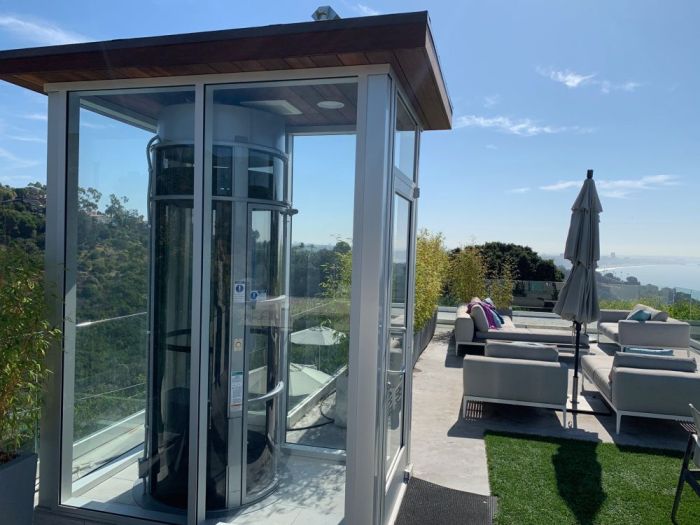
Source: vacuumelevators.com
Exterior elevator design is crucial; it’s not just about functionality but significantly impacts a building’s overall aesthetic appeal and brand identity. The visual impact of these elevators, often a prominent architectural feature, directly influences the perception of the entire structure. Careful consideration of materials, finishes, and integration with the building’s style is paramount.
Exterior Elevator Designs for Different Building Types
This section details three distinct exterior elevator designs tailored to modern office buildings, luxury hotels, and retail complexes. Each design prioritizes functionality while reflecting the unique character of its intended environment.
Modern Office Building: Imagine a sleek, glass-encased elevator rising alongside a modern glass and steel skyscraper. The elevator’s cabin is made of polished stainless steel, with tinted glass panels offering panoramic views. The exterior frame is constructed from powder-coated aluminum, matching the building’s color scheme. Subtle LED lighting integrated into the frame provides soft illumination at night, enhancing its visibility and modern aesthetic.
The overall design aims for a clean, minimalist look that complements the building’s contemporary architecture.
Luxury Hotel: For a luxury hotel, the exterior elevator design might incorporate more ornate details and luxurious materials. Picture an elevator with a bronze-finished frame and panels of textured glass, etched with a subtle repeating pattern. The cabin interior features rich wood paneling, plush seating, and indirect lighting to create a warm and inviting atmosphere. The elevator’s design might subtly incorporate elements from the hotel’s overall branding, such as a specific color or motif.
This design exudes elegance and sophistication, aligning with the high-end image of the hotel.
Retail Complex: An exterior elevator in a bustling retail complex needs to be both visually appealing and durable. Envision an elevator with a brightly colored, composite panel exterior. The panels could feature bold graphics or a dynamic light show, creating a visually engaging focal point. The materials used would need to be resistant to weathering and vandalism.
The design could incorporate interactive elements, such as a digital display showing information about the stores within the complex. This design prioritizes vibrancy and visual impact, attracting attention and encouraging shoppers to use the elevator.
Innovative Design Solutions for Exterior Elevators
Several innovative design solutions can significantly enhance both the aesthetic appeal and functionality of exterior elevators. These solutions often involve integrating technology and sustainable materials to create unique and impactful designs.
“The integration of solar panels into the elevator’s exterior can not only provide a sustainable energy source but also add a visually interesting textural element to the design.”
“Using transparent or translucent materials for the elevator car allows for views of the surrounding cityscape, transforming the ride into a unique experience. This design element is particularly effective in high-rise buildings with stunning views.”
“Kinetic energy recovery systems can be incorporated into the elevator’s mechanics, reducing energy consumption and contributing to a more environmentally friendly design.”
Exterior Elevator Design and Building Architecture
Exterior elevator design is intrinsically linked to the overall architectural style and branding of a building. A well-integrated elevator design enhances the building’s visual appeal and reinforces its architectural theme. For instance, a modern glass elevator would complement a contemporary skyscraper, while a more traditional elevator design might be appropriate for a historic building. The elevator’s design should seamlessly blend with the building’s facade, creating a cohesive and visually pleasing whole.
The choice of materials, finishes, and architectural details should reflect the building’s intended purpose and brand identity, ensuring a harmonious and impactful overall design.
Cost and Budget Considerations
Installing a commercial exterior elevator is a significant investment, requiring careful planning and budgeting to avoid unexpected expenses. Understanding the various cost components and factors influencing the final price is crucial for a successful project. This section breaks down the typical costs and provides guidance on creating a realistic budget.
The total cost of a commercial exterior elevator project encompasses several key areas, each contributing significantly to the overall expense. Accurate estimation requires considering all aspects, from initial purchase to ongoing maintenance.
Cost Breakdown
The costs associated with commercial exterior elevators can be categorized into several key areas. These costs vary widely depending on several factors, as detailed in the following sections. It’s crucial to obtain multiple quotes from reputable elevator companies to get a comprehensive understanding of the price range.
- Purchase Price: This is the cost of the elevator itself, varying greatly depending on size, capacity, features, and manufacturer. Expect to pay anywhere from $50,000 to well over $200,000 for a standard unit. High-end models with advanced features can cost significantly more.
- Installation Costs: This includes labor, permits, site preparation (including potential foundation work), and electrical and mechanical connections. Installation costs typically range from 20% to 40% of the elevator’s purchase price, sometimes exceeding it in complex installations.
- Maintenance and Repair: Ongoing maintenance contracts are essential for ensuring the elevator’s safety and longevity. Annual maintenance contracts typically cost between 1% and 3% of the elevator’s initial purchase price, with repair costs varying depending on the issue.
- Permits and Inspections: Obtaining necessary building permits and undergoing inspections adds to the overall cost. Permitting fees vary by location and the complexity of the project.
- Freight and Delivery: The cost of transporting the elevator to the installation site should also be factored in. This is particularly relevant for locations that are geographically remote or difficult to access.
Factors Influencing Cost
Several factors significantly impact the final cost of a commercial exterior elevator project. Careful consideration of these factors during the planning phase is crucial for accurate budgeting.
- Elevator Size and Capacity: Larger elevators with higher weight capacities naturally cost more. The size of the elevator shaft and the required counterweights also affect the cost.
- Features and Technology: Advanced features like automatic doors, emergency communication systems, and sophisticated control systems increase the purchase price. Options such as specialized finishes or custom designs also add to the cost.
- Location: Installation in remote or difficult-to-access locations will increase labor and transportation costs. Local regulations and permitting requirements can also influence the overall expense.
- Building Design and Structure: The existing building’s structure and design can influence installation complexity, potentially increasing costs. Modifications to the building might be necessary, adding to the expense.
Budgeting for an Exterior Elevator Project
Creating a realistic budget involves a methodical approach. It’s recommended to work with an elevator consultant and contractor to obtain accurate estimates for all aspects of the project.
A realistic budget should include:
- Detailed Cost Estimates: Obtain multiple detailed quotes from reputable elevator companies, clearly outlining all costs.
- Contingency Fund: Include a contingency fund of at least 10-15% of the total estimated cost to cover unexpected expenses or delays.
- Long-Term Maintenance Costs: Factor in annual maintenance costs and potential repair expenses over the elevator’s lifespan.
- Financing Options: Explore financing options such as loans or leases to manage the upfront costs.
For example, a mid-sized exterior elevator for a small commercial building might have a total cost ranging from $100,000 to $150,000, including installation and a basic maintenance contract. A larger, high-rise installation could easily exceed $500,000.
Accessibility and ADA Compliance
Ensuring that commercial exterior elevators meet the requirements of the Americans with Disabilities Act (ADA) is crucial for providing equitable access to buildings for individuals with disabilities. Failure to comply can result in significant legal and financial repercussions. This section details the key ADA requirements and design features that promote accessibility.
The ADA Standards for Accessible Design provide comprehensive guidelines for making buildings and facilities accessible to people with disabilities. These standards cover various aspects of elevator design and operation, aiming to ensure safe and convenient use by individuals with mobility impairments, visual impairments, and other disabilities.
ADA Requirements for Exterior Elevators
The ADA mandates specific design features for elevators to ensure accessibility. These include requirements for button placement, call button size and spacing, audible and visual signals, and cabin dimensions. For exterior elevators, additional considerations may be necessary due to environmental factors like weather protection and visibility. For example, the control panel must be positioned within easy reach for wheelchair users, and emergency communication systems must be readily accessible and functional.
All signage must be clear, concise, and easy to read, including braille and tactile characters. Furthermore, the elevator car itself must be large enough to accommodate a wheelchair user and a companion.
Design Features Enhancing Accessibility
Several design features enhance the accessibility of commercial exterior elevators. Ramps leading to the elevator platform can improve accessibility for wheelchair users and those with mobility issues, provided the ramp meets ADA gradient requirements. Large, clearly marked call buttons with tactile markings and audible signals are essential for visually impaired users. These buttons should be spaced appropriately for ease of use, including for individuals with limited dexterity.
Signage should clearly indicate the elevator’s location and operating instructions, using both visual and tactile cues. Emergency communication systems, including emergency telephones and two-way communication systems, are crucial for ensuring the safety and well-being of all users. The elevator cabin should have ample space for wheelchairs, and adequate handrails should be provided for support. Adequate lighting within and around the elevator ensures safe and convenient use at all times of day.
Obtaining ADA Certification
Obtaining ADA certification for an exterior elevator installation typically involves a multi-step process. First, the elevator’s design and installation must fully comply with the ADA Standards for Accessible Design. This requires working with architects, engineers, and elevator contractors experienced in ADA compliance. Detailed plans and specifications should be reviewed by an accessibility consultant to ensure that all aspects of the design meet the standards.
Once the elevator is installed, an accessibility inspection must be conducted by a qualified professional to verify compliance. This inspection may involve checking button placement, signage, cabin dimensions, and emergency communication systems. Finally, documentation demonstrating compliance with the ADA Standards must be submitted to the appropriate authorities. This documentation typically includes design drawings, inspection reports, and certifications from qualified professionals.
The specific requirements for obtaining ADA certification may vary depending on local regulations and jurisdiction. In many cases, it is beneficial to engage with an ADA consultant throughout the design and construction process to minimize potential issues and streamline the certification process. Failing to comply can lead to costly retrofits and legal challenges.
Environmental Impact: Commercial Exterior Elevators
Commercial exterior elevators, while offering convenient vertical transportation, have a significant environmental footprint stemming from their energy consumption and material use throughout their lifecycle. Understanding this impact and implementing sustainable practices is crucial for responsible building design and operation.The primary environmental concern is energy consumption. Exterior elevators, often exposed to the elements, require more energy for heating and cooling than interior counterparts.
Furthermore, the hoisting mechanism itself consumes considerable power, particularly in high-rise buildings. The materials used in construction, including steel, concrete, and various components, also contribute to the overall environmental impact through their extraction, manufacturing, and transportation. The disposal of these materials at the end of the elevator’s lifespan presents further environmental challenges.
Energy Consumption and Reduction Strategies
Minimizing energy consumption is paramount. High-efficiency motors, regenerative braking systems (which recapture energy during descent and feed it back into the power grid), and optimized control systems can significantly reduce energy usage. Employing energy-efficient lighting within the elevator cab and utilizing solar panels to power certain aspects of the elevator’s operation are further strategies for reducing the environmental footprint.
For example, a building in Seattle, Washington, incorporated solar panels to power the lighting and some control systems of its exterior elevators, reducing their energy consumption by approximately 15%.
Material Selection and Sustainable Practices
The selection of environmentally friendly materials is vital. Using recycled steel and concrete in the elevator’s construction reduces the demand for newly extracted resources. Choosing low-VOC (volatile organic compound) paints and finishes minimizes air pollution during construction and operation. Furthermore, prioritizing durable and long-lasting materials extends the elevator’s lifespan, reducing the frequency of replacements and associated environmental impacts.
The use of sustainable wood products, where applicable, and the incorporation of recycled components are further steps toward environmentally responsible design.
Lifecycle Management and Waste Reduction
Minimizing the environmental footprint extends beyond the initial construction phase. Regular maintenance ensures optimal energy efficiency and prolongs the elevator’s operational life. A comprehensive maintenance plan, including preventative measures, can significantly reduce energy waste and the need for premature replacements. At the end of the elevator’s lifespan, responsible dismantling and recycling of components are crucial. Planning for disassembly and material recovery during the design phase facilitates efficient and environmentally sound disposal.
This can include separating different materials for recycling and repurposing suitable components for other applications. Several European countries have implemented strict regulations and incentives for the responsible recycling of construction materials, including elevator components.
Concluding Remarks
Commercial exterior elevators are more than just vertical transportation; they’re integral components of modern buildings, impacting aesthetics, functionality, safety, and accessibility. Understanding their complexities—from initial design and installation to ongoing maintenance and compliance—is crucial for successful building projects. By carefully considering the various factors discussed in this guide, stakeholders can ensure that their exterior elevators are not only safe and efficient but also contribute positively to the overall building design and its environmental footprint.
Choosing the right type of elevator, implementing appropriate safety measures, and prioritizing regular maintenance are key to maximizing the longevity and performance of this critical building system.
Questions and Answers
What is the average lifespan of a commercial exterior elevator?
The lifespan varies greatly depending on factors like maintenance, usage, and environmental conditions, but generally ranges from 25 to 30 years.
How often should a commercial exterior elevator be inspected?
Regular inspections are typically required annually, or more frequently depending on local regulations and usage.
What are the common causes of elevator breakdowns?
Common causes include mechanical wear and tear, electrical malfunctions, and issues with the control system.
Are there tax incentives for installing energy-efficient exterior elevators?
Some regions offer tax incentives or rebates for energy-efficient building upgrades, including elevators. Check with local authorities for details.
Can exterior elevators be retrofitted into existing buildings?
Yes, but it’s a complex undertaking requiring careful planning and structural assessments.